Vacuum Circuit Breaker (VCB) Assembly Production Line
RGV type assembly line, used for indoor VCB assembly production
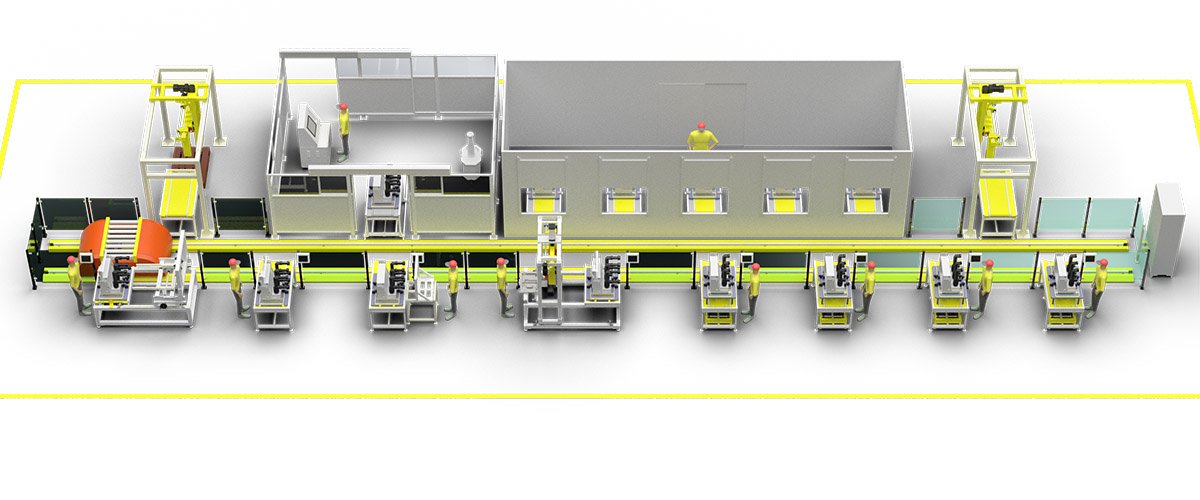
The RGV-type assembly line for vacuum circuit breakers is an efficient and reliable method of power equipment production. It utilizes automated technology and precision machinery to ensure the quality and performance of vacuum circuit breakers. By optimizing the production process and implementing strict quality control, the RGV assembly line enhances production efficiency, reduces labor costs, and guarantees product consistency and reliability. The application of this assembly line is of significant importance for improving the stability and safety of power systems.
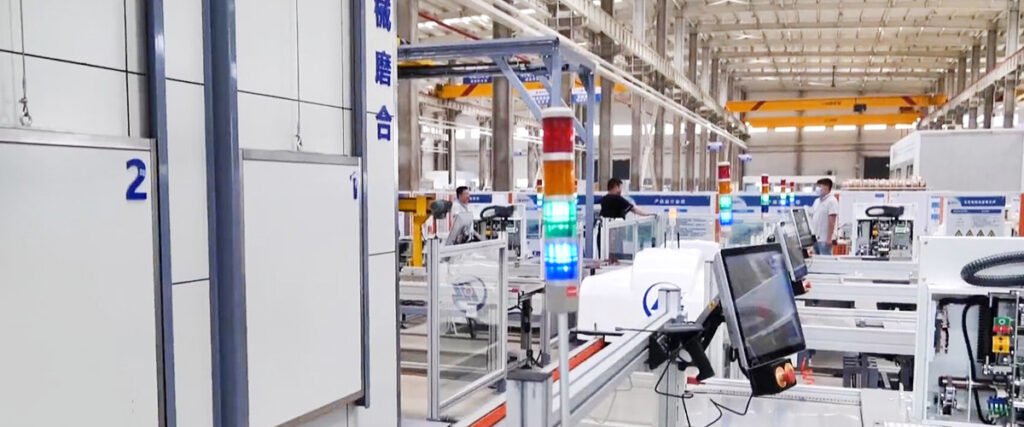
Vacuum Circuit Breaker (VCB) Assembly and Calibration
Assemble the potted vacuum arc chamber into the breaker mechanism and attach other necessary components, such as the spring energy storage operating mechanism and control units. After assembly, preliminary calibration is performed to ensure all mechanical parts move smoothly and electrical connections are correct.
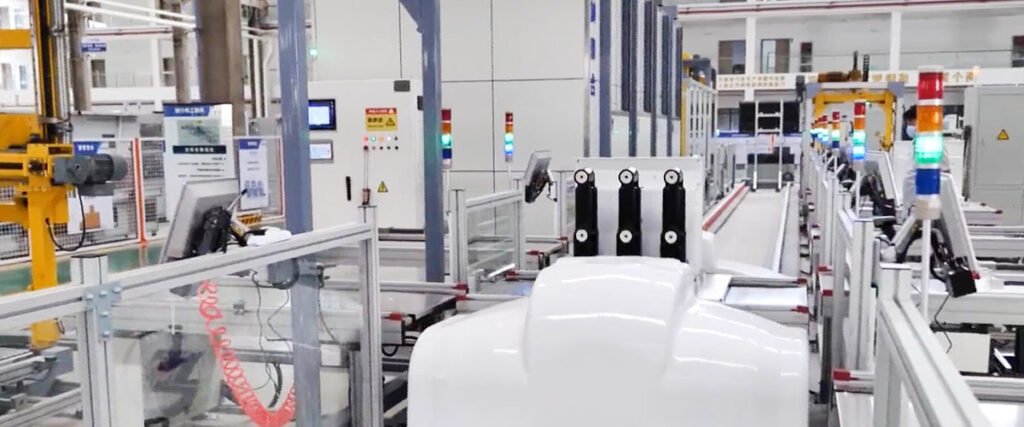
Vacuum Circuit Breaker (VCB) Performance Testing A series of performance tests are conducted on the assembled vacuum circuit breaker, including AC withstand voltage test, lightning impulse withstand voltage test, loop resistance measurement, temperature rise test, mechanical life test, electrical life test, short time withstand current and peak withstand current test, and short-circuit current making and breaking test.
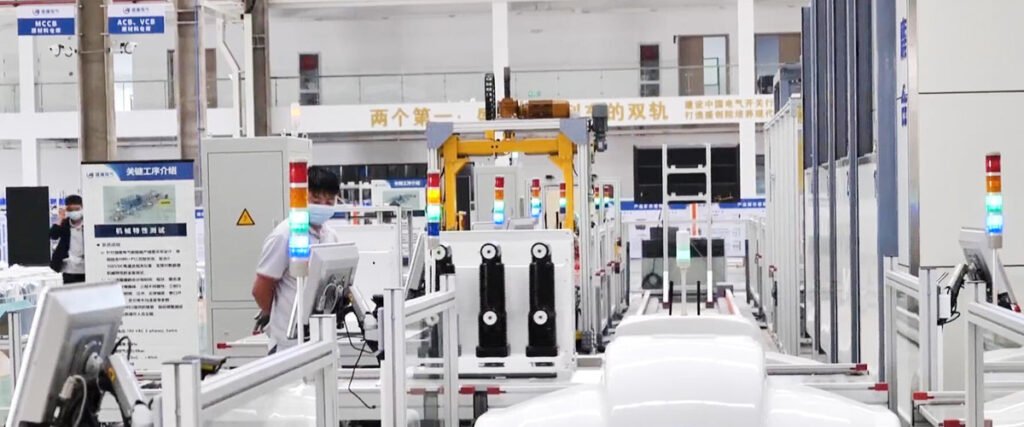
Atlas of Vacuum Circuit Breaker Assembly Lines from Design to Manufacturing
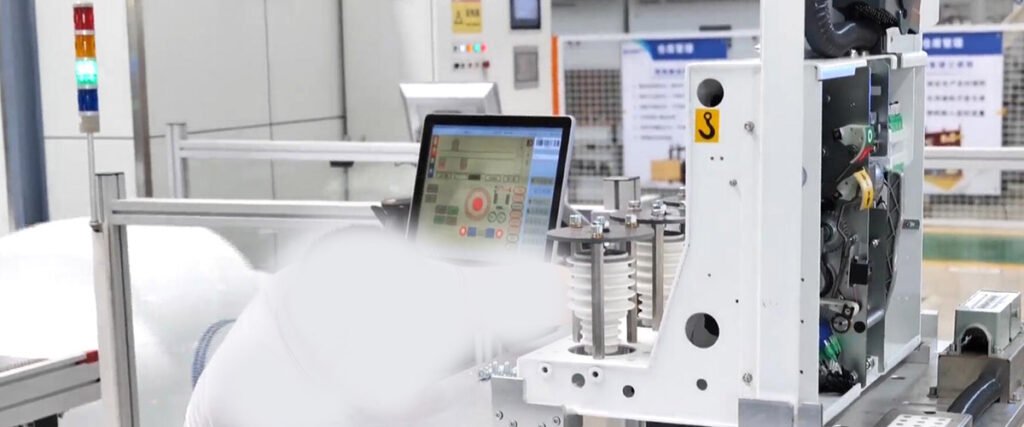
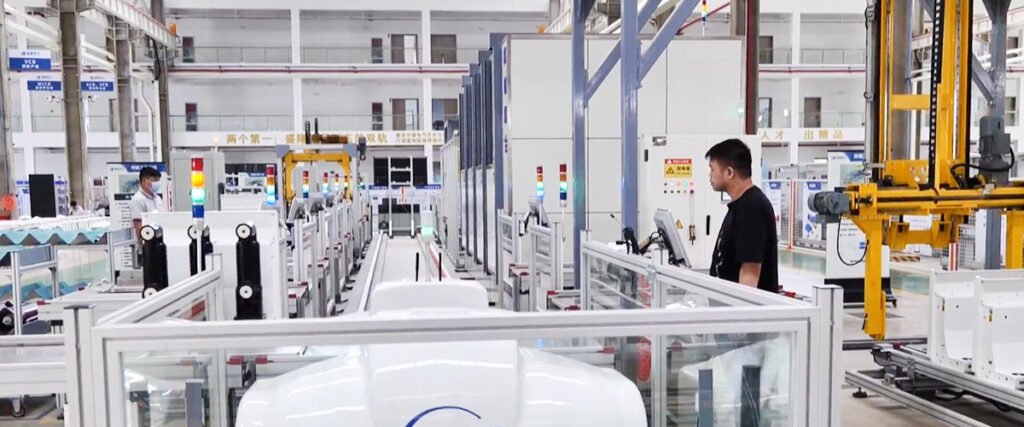


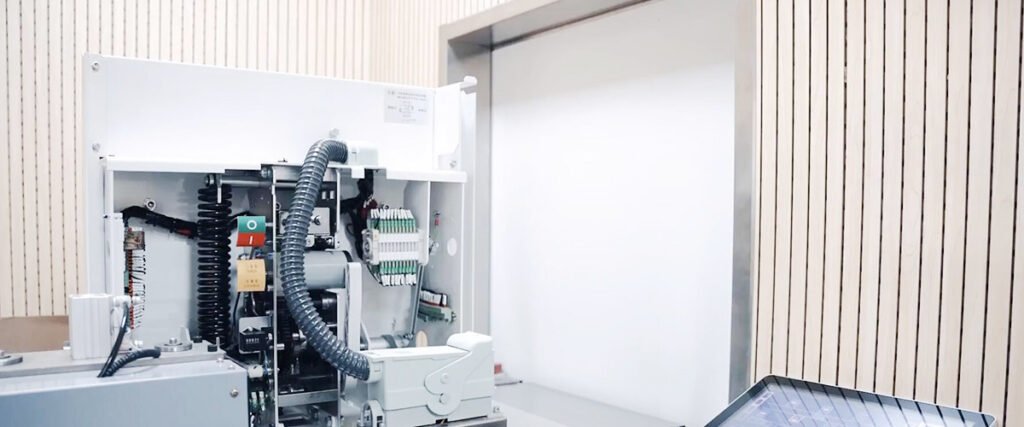
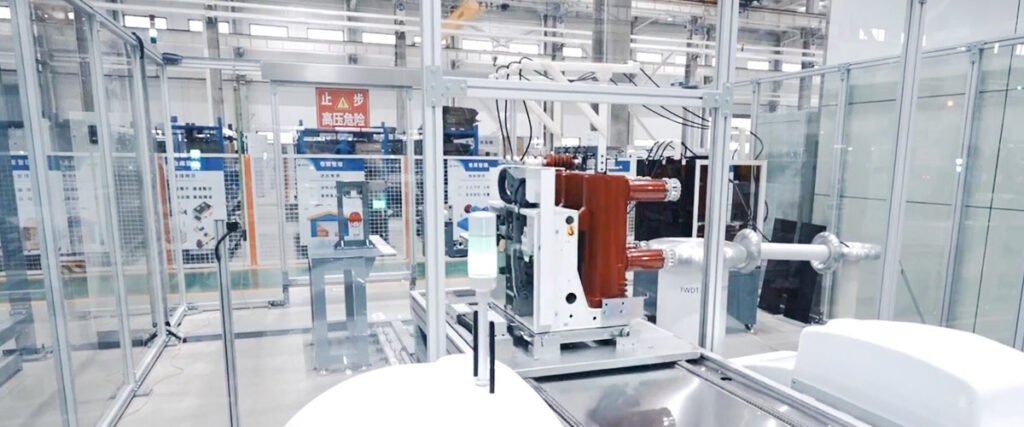
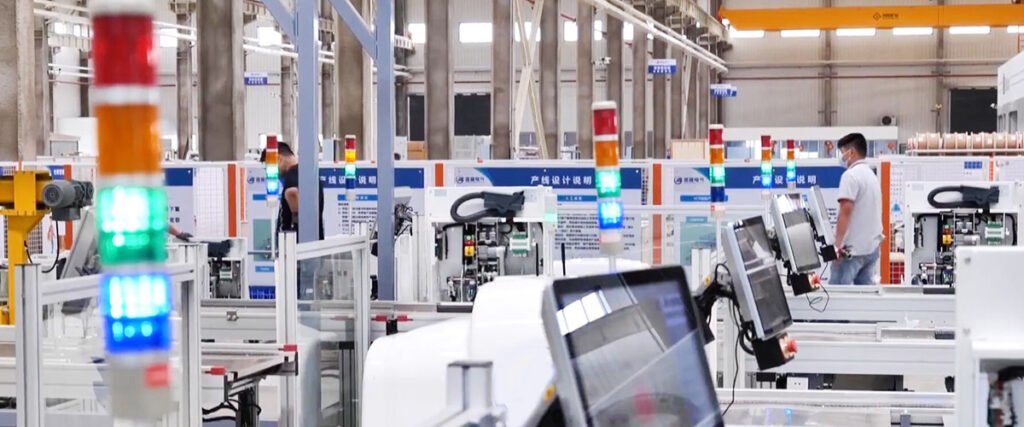
Three-dimensional (3D) design offers significant advantages in the production line plan for vacuum circuit breakers: it enhances the precision and visualization of the design, simplifies the modeling and analysis of complex components; by simulating and optimizing the production process, it improves efficiency and product quality; it facilitates rapid iteration and design validation, shortening the product development cycle; meanwhile, it facilitates cross-department collaboration, ensuring consistency between design intent and production reality, reducing error rates and rework costs.
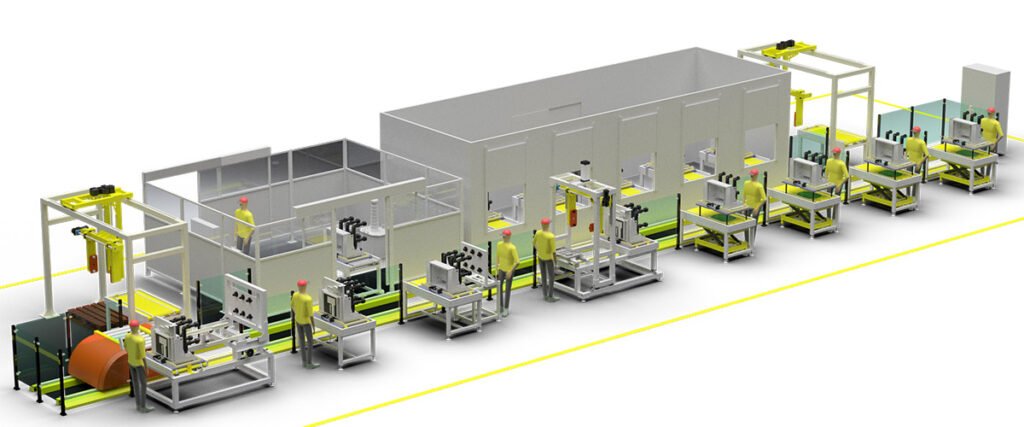