Outdoor vacuum circuit breaker production line and testing points
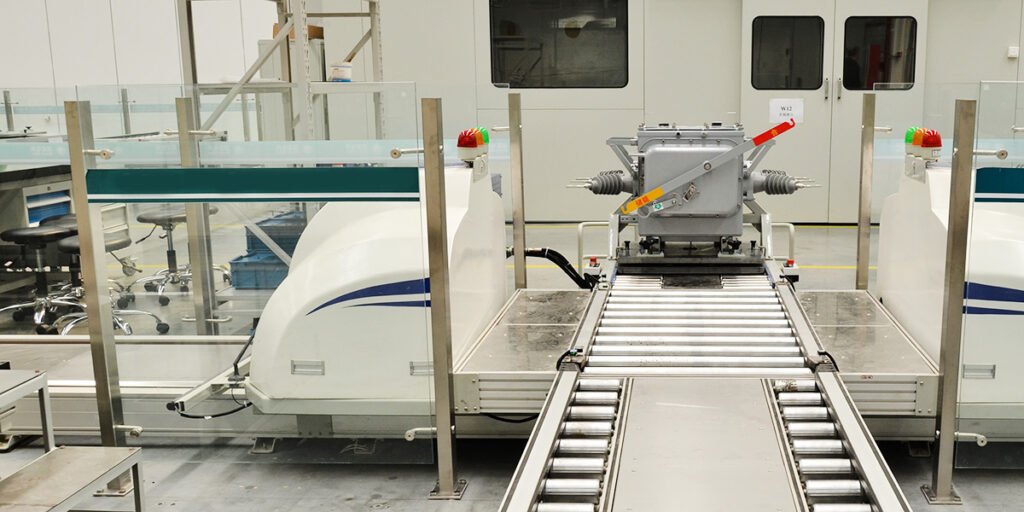
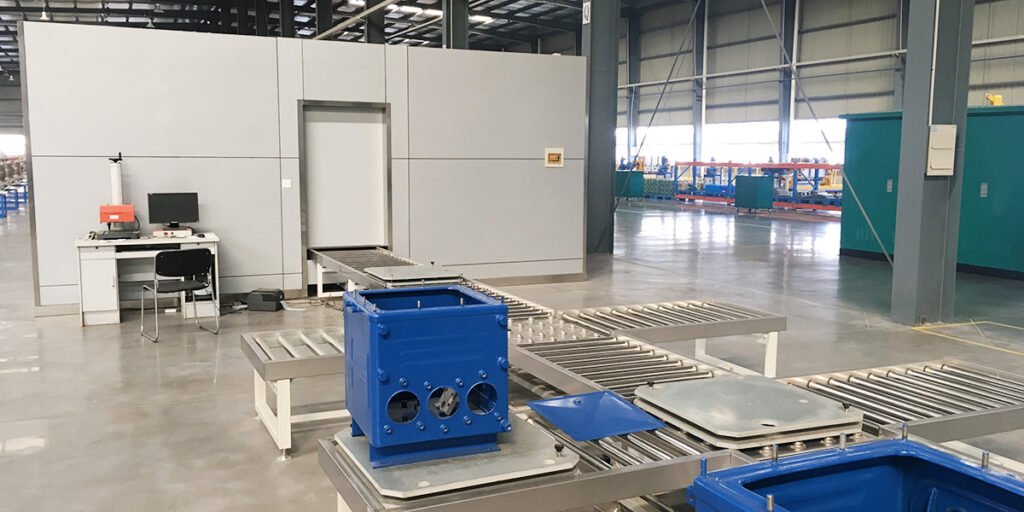
The production line and testing of outdoor vacuum circuit breakers are critical to ensuring the quality and performance of the products meet standard requirements. Here are some key points for production and testing:
- Production Environment Control:
- Ensure the cleanliness of the production environment to prevent dust and contaminants from affecting the assembly and performance of the vacuum circuit breaker.
- Control the temperature and humidity in the production area to meet the technical requirements for assembling vacuum circuit breakers.
- Component Quality Inspection:
- Conduct quality checks on all components entering the production line to ensure there are no damaged or non-compliant parts.
- Perform vacuum degree testing on key components such as vacuum arc chambers to ensure they meet specified vacuum standards.
- Assembly Process Monitoring:
- Assemble strictly according to the assembly manual to ensure each step complies with design and process requirements.
- Monitor and record key steps in the assembly process, such as the alignment of contact points and the installation of insulators.
- Mechanical Characteristics Testing:
- Conduct mechanical characteristics tests on assembled vacuum circuit breakers, including opening and closing times, bounce time, and low-voltage operation.
- Ensure test results meet product technical specifications and customer requirements.
- Electrical Performance Testing:
- Perform insulation resistance tests, loop resistance tests, and grounding resistance tests to ensure the safety and reliability of electrical connections.
- Conduct AC withstand voltage tests to verify the insulating strength of the vacuum circuit breaker at rated voltage.
- Vacuum Degree Testing:
- Test the vacuum degree of vacuum arc chambers in the vacuum circuit breaker using methods such as magnetic control discharge, pulse method, or other effective methods.
- Ensure the vacuum degree meets national standards and industry requirements to guarantee the insulation and arc-quenching performance of the circuit breaker.
- Environmental Adaptability Testing:
- Evaluate the environmental adaptability of the vacuum circuit breaker through temperature cycling tests, salt spray tests, etc., to assess its performance and durability under various environmental conditions.
- Confirm that the product can adapt to the various climates and environmental conditions of outdoor installation.
- Safety Performance Assessment:
- Assess the safety performance of the vacuum circuit breaker, including operational safety and the effectiveness of protective measures.
- Ensure the product complies with relevant safety standards and regulatory requirements.
- Quality Control and Documentation:
- Implement strict quality control measures during production and testing to ensure product quality.
- Record all data from production and testing for traceability and quality analysis.
- Final Inspection Before Shipment:
- Conduct a comprehensive final inspection before the product leaves the factory, including visual inspection, identification verification, and functional validation.
- Ensure all documentation and certificates are complete for customer acceptance.
By following these production and testing points, the production line for outdoor vacuum circuit breakers can operate efficiently, and the quality and performance of the products can meet the highest standards.