Indoor vacuum circuit breaker assembly production line
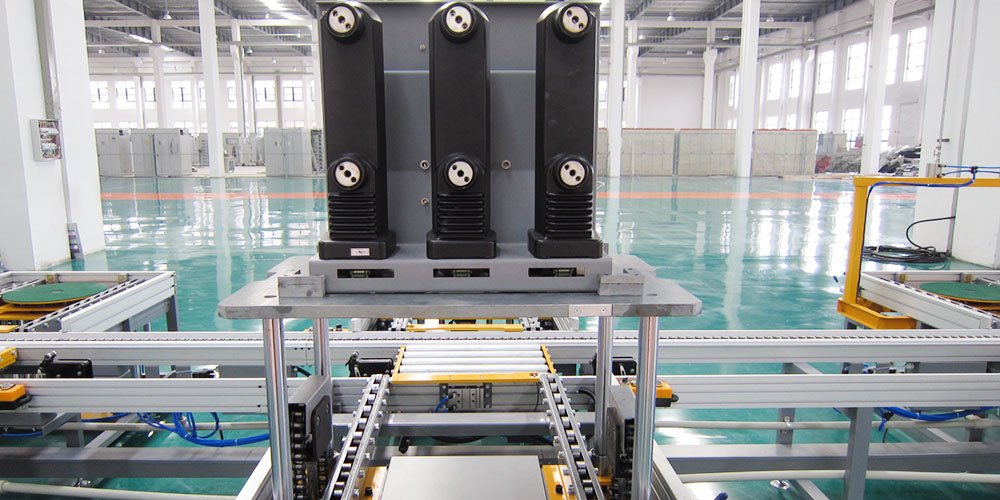
The assembly production line process for indoor vacuum circuit breakers is a complex sequence of steps designed to ensure the quality and performance of the product.
- Design and Preparation:
- Based on product design drawings and technical specifications, prepare the necessary raw materials and components, such as vacuum arc chambers, operating mechanisms, and conductive parts.
- Ensure all components meet quality standards and specification requirements.
- Component Machining:
- Process the raw materials into parts for the circuit breaker, such as cutting, stamping, bending, etc.
- Use CNC machines and other precision machining equipment to ensure accuracy.
- Assembly:
- Assemble the machined parts according to design requirements, including installing the vacuum arc chamber, securing the operating mechanism, and connecting conductive parts.
- Ensure all parts are correctly installed and securely connected.
- Mechanical Adjustment:
- Mechanically adjust the assembled circuit breaker to ensure the flexibility and accuracy of the operating mechanism.
- Adjust the contact gap to meet technical specifications.
- Electrical Testing:
- Conduct electrical performance tests on the circuit breaker, including insulation resistance tests, conductivity tests, and vacuum level tests for the vacuum arc chamber.
- Ensure all electrical parameters comply with standard requirements.
- Functional Testing:
- Perform functional tests by simulating the opening and closing operations of the circuit breaker to verify its operational performance and reliability.
- Check that the circuit breaker’s energy storage function and locking function are normal.
- Quality Inspection:
- Conduct appearance and quality inspections on the completed circuit breaker, ensuring all screws are tightened, and the nameplate information matches the actual components’ specifications.
- Check that packaging and accessories are complete and that the product’s appearance is undamaged and aesthetically pleasing.
- Typical Fault Analysis and Troubleshooting:
- Analyze typical faults that may occur during testing and develop corresponding troubleshooting methods.
- Ensure that the fault handling mechanism on the production line is effective to reduce production interruptions.
- Final Inspection:
- In the final inspection stage, conduct a final check on the circuit breaker, including secondary circuit testing and automatic test bench line testing.
- Ensure the circuit breaker does not damage the control module of the test bench in case of a strong electrical circuit connection error.
- Packaging and Shipping:
- After all inspections are completed, properly package the circuit breaker to protect the product from damage during transportation.
- Prepare shipping documents and dispatch the product to customers or inventory.