Gas Insulated Switchgear (GIS) Assembly Production line
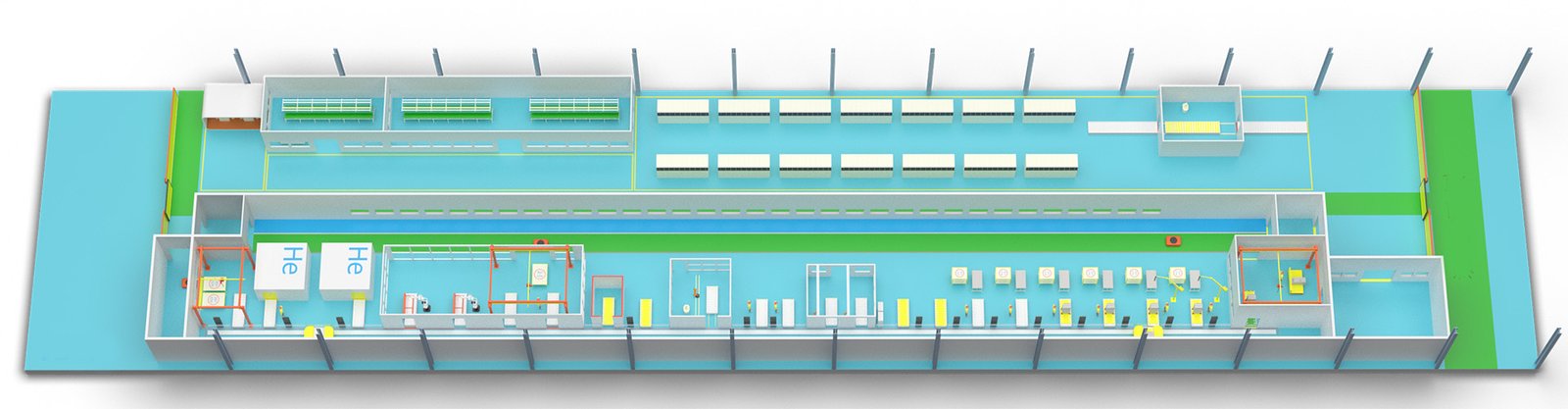
Utilizing an assembly line and MES (Manufacturing Execution System) in the production and testing of Gas Insulated Switchgear (GIS) offers numerous advantages. The assembly line streamlines the manufacturing process, ensuring consistent quality and reducing the likelihood of human error. It allows for a clear division of labor, enhancing efficiency and throughput. The MES system provides real-time data collection and analysis, enabling better monitoring of production status and quality control. It facilitates just-in-time inventory management, reducing storage costs and material waste. Furthermore, MES supports traceability and compliance with industry standards, which is critical for high-voltage equipment like GIS. The integration of MES with the assembly line leads to a more flexible and adaptive production environment, capable of responding quickly to changes in demand or design specifications. Overall, the combination of an assembly line and MES system results in a more reliable, efficient, and cost-effective production process for GIS.
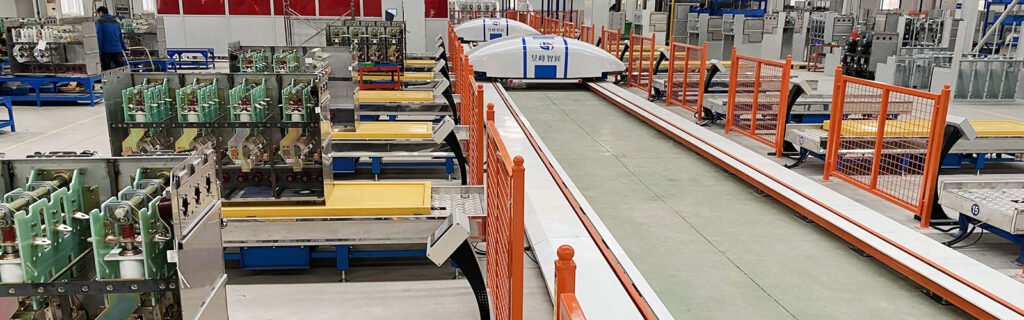
Gas Insulated Switchgear (GIS) structure and production testing process are key to ensuring its high performance and reliability. Here is the general information on GIS:
Structural Features
- Modular Design: GIS equipment adopts a modular design, which facilitates expansion and adaptation to different application requirements.
- Safe Encapsulation: All high-voltage components, such as circuit breakers, disconnectors, grounding switches, etc., are encapsulated within a metal housing, enhancing safety.
- High Gas Tightness: GIS equipment has good gas tightness, ensuring the stability of the internal SF6 gas, thereby safeguarding insulation and arc-extinguishing performance.
- Ease of Operation and Maintenance: The design takes into account the convenience of operation and ease of maintenance, including motor-operated mechanisms and the possibility of manual emergency operation.
- Independent Gas Compartments: Each gas compartment is independent, without gas connections, simplifying gas handling and maintenance.
Production Testing Process
- Factory Assembly: GIS equipment is assembled in the factory to ensure precise fitting of components and overall stability.
- Gas Filling and Testing: SF6 gas is filled in the enclosed gas compartments, and leakage tests are conducted to ensure the sealing and purity of the gas.
- Operating Mechanism Testing: The motor-operated operating mechanisms are tested to ensure reliable operation under normal and emergency conditions.
- Insulation Performance Testing: The insulation performance of GIS is tested, including partial discharge testing and insulation resistance testing.
- Functional Testing: All functions of GIS are tested, including the opening and closing operations of circuit breakers, operations of grounding switches, etc.
- Type Testing: Type testing is conducted according to International Electrotechnical Commission (IEC) standards to verify the performance of GIS equipment under extreme conditions.
- Pre-Delivery Testing: Comprehensive testing is carried out before delivery of GIS to ensure it meets customer requirements and standards.
Through these rigorous production testing processes, Gas Insulated Switchgear can ensure high performance, high reliability, and long service life.