Ring main unit assembly production line process flow
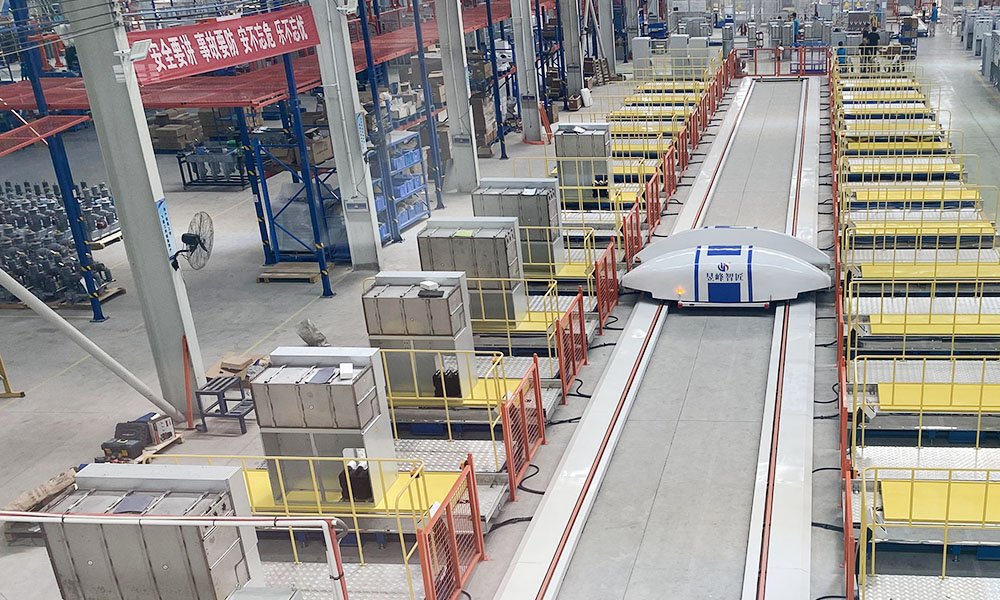
The assembly process flow of a ring main unit (RMU) assembly line is a complex and precise procedure that involves multiple steps and technical stages to ensure the quality and performance of the RMU meet standard requirements. Based on the search results provided.
Ring main unit assembly production line process flow:
1. Initial Preparation Phase
- Material Preparation: First, various raw materials required for the RMU, including bent sheets, cut plates, and other fasteners like studs, need to be prepared.
- Material Handling: Use a handling device (such as a robotic arm or automated conveyor system) to transport the plates and fasteners to the corresponding workstations.

2. Welding and Processing Phase
- Stud Welding: In the stud welding station, plates that require stud welding are transported to a fixed position where a stud welding device welds the studs onto the plates.
- Plate Grinding: In the grinding station, plates that need grinding are processed, such as grinding the hole positions on the cut plates to remove burrs.
- Assembly and Spot Welding: Transport the processed plates to the workbench for assembly and manual spot welding, forming the preliminary structure of the RMU.

3. Closed Welding and Inspection Phase
- Closed Welding: Transport the spot-welded plates to the closed welding station, where a closed welding device performs full welding on the seams to ensure the structural strength and sealing of the RMU cabinet.
- Performance Testing: Conduct mechanical characteristic inspections, semi-finished product performance tests, finished product performance tests, gas tank leak detection, and power frequency withstand voltage tests in the RMU comprehensive performance testing system to ensure the product’s performance meets standards.
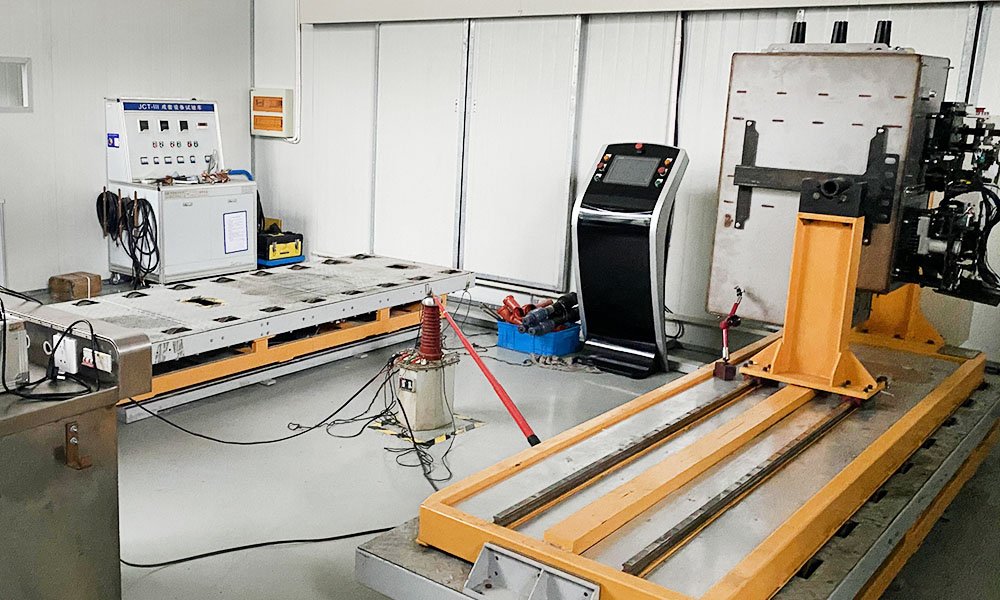
4. Cleaning and Final Inspection Phase
- Cleaning: Use a cleaning device (such as an ultrasonic cleaning machine) to clean the welded RMU cabinet to remove welding residues and oil.
- Final Inspection: After cleaning, conduct a final inspection of the RMU, including visual inspection, dimension measurement, and electrical performance testing, to ensure product quality.
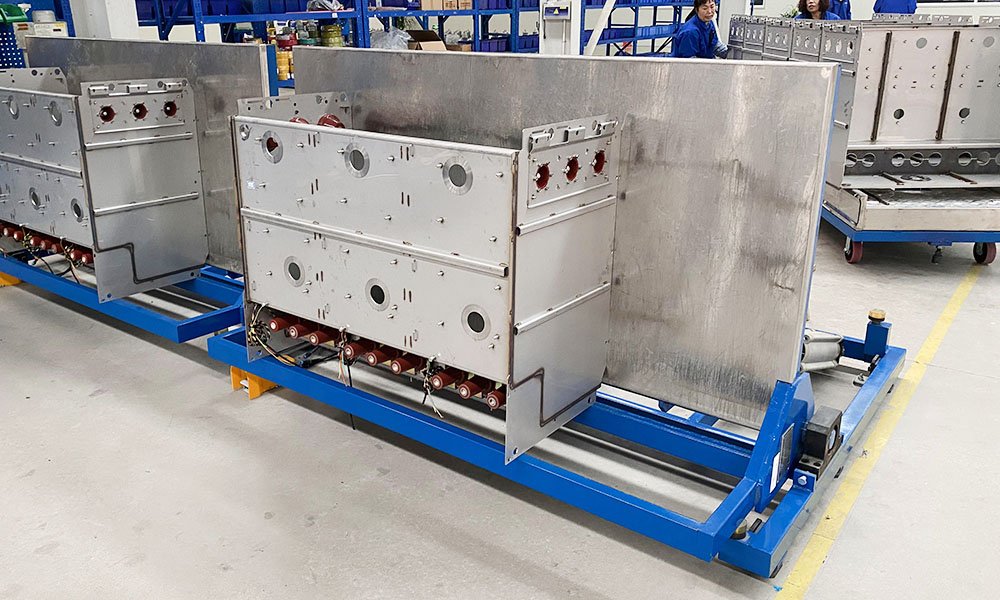
5. Assembly and Commissioning Phase
- Assembly: Install various components (such as switches, circuit breakers, isolation switches, etc.) onto the cabinet and make necessary adjustments and alignments.
- Commissioning: Perform electrical commissioning on the assembled RMU to ensure all electrical components are functioning correctly and meet safety and performance requirements.

6. Outgoing and Delivery Phase
- Labeling: Attach necessary labels to the RMU, including product model, production batch, inspection certification, etc.
- Finalization: Once all assembly and testing are completed, the RMU can be finalized for shipment and delivery.
7. Data Management and Traceability
- Information Collection: During the production process, collect production data, including assembly and welding data, using devices like RFID readers and barcode guns, and upload it to the production line control management system.
- Quality Traceability: Achieve management and traceability of product quality through information systems (such as ERP, WMS, etc.) to ensure the traceability of product quality.
Through the above process, the RMU assembly line can efficiently and safely complete the assembly of RMUs while ensuring the quality and performance of the products meet industry standards.