Process flow of indoor vacuum circuit breaker production line
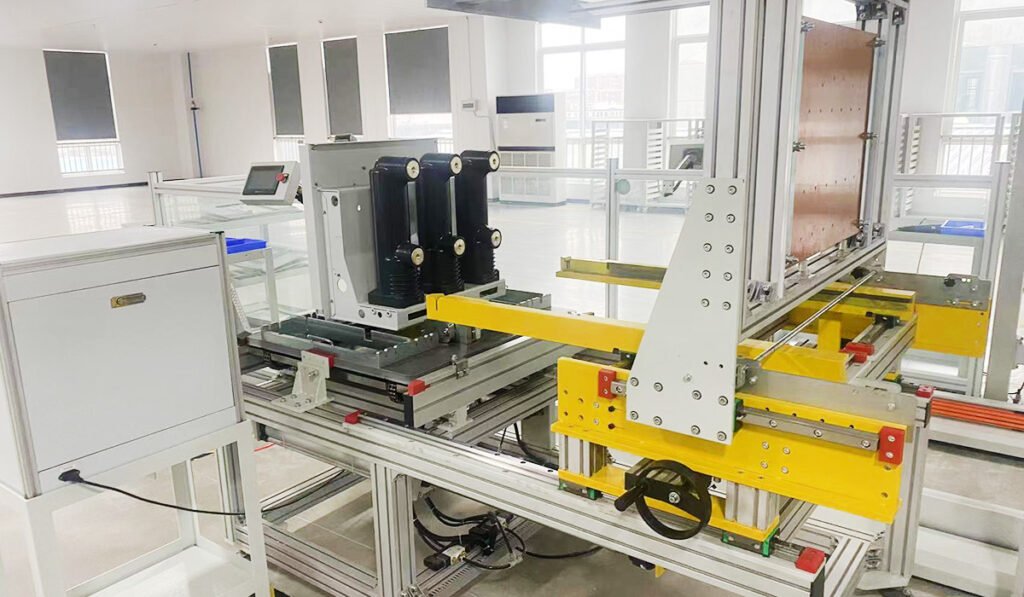
The production line process for indoor vacuum circuit breakers typically includes several steps, from design, assembly, to testing and quality control. Here is an overview of the production line process for vacuum circuit breakers based on the information provided by Hva7:
- Secondary Circuit Assembly: In this process, operators verify the assembly flow card to confirm the secondary components required for assembly and their quantities, then proceed with the wiring work.
- Operating Voltage Setting: The circuit breaker is moved from the production line to the workbench, connected to an aviation socket, and the standard operating voltage is set according to the assembly flow card.
- Sensor Connection: The three-phase sensor is connected to the main drive connecting pin of the circuit breaker to ensure smooth up and down movement without any jamming.
- Component Processing: This includes surface treatment, assembly and sealing, and final inspection, involving the provision of pure water and wastewater treatment.
- Material Quality Control: Strict control over smelting temperature, gas content, impurity and nitride content, as well as material density, while also controlling the conductivity performance and metallographic structure.
- Machining: Advanced CNC-controlled machining of contact heads and deep processing technology with a pressing capacity of 1,000 kN are utilized.
- Surface Treatment: Automated plating equipment is used for surface treatment.
- Assembly: Assembly is carried out in a cleanroom environment, followed by thorough dust cleaning.
- Quality Assurance: Automatic AC and impulse withstand voltage equipment is used for testing, along with a special internal pressure measurement process for leak detection.
- Performance Testing: Various performance tests are conducted on the circuit breaker, including breaking current capacity, insulation strength, vacuum level, contact resistance, chopping current value, re-ignition rate, and leak rate.
- Final Inspection: After all assembly and testing are completed, a final inspection is carried out to ensure the product meets quality standards.
Please note that the above steps are organized based on the information from the resources provided, and the specific process may vary depending on the actual operations of different manufacturers.