Dry type transformers assembly line process
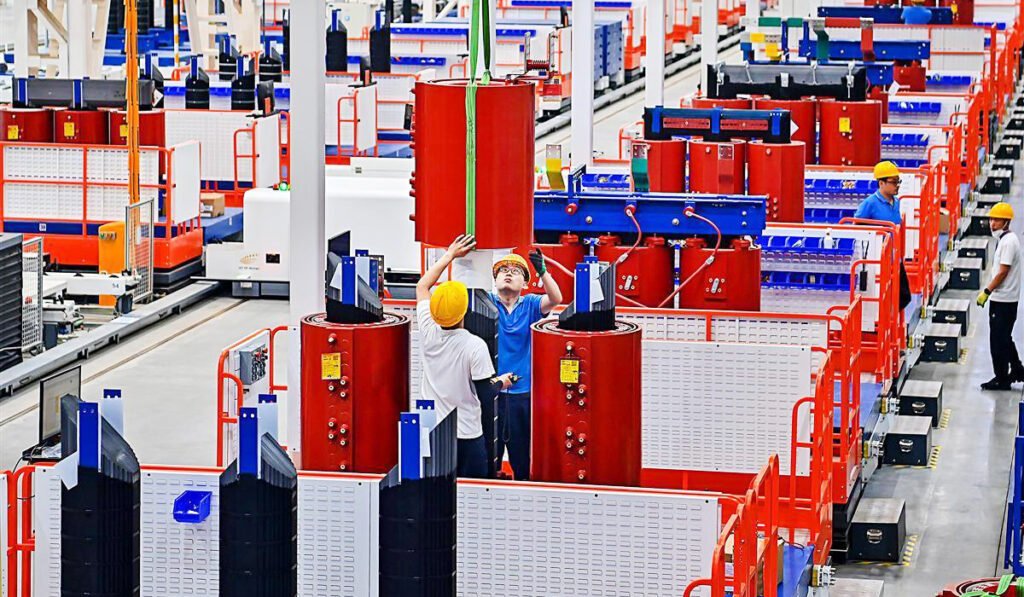
The assembly process of dry type transformers is a complex procedure that directly affects the performance, safety, and operational stability of the transformer.
Preparation Before Assembly
Before starting the assembly, ample preparation is required, including:
- Material and Tool Preparation: Based on the design requirements and assembly process of the transformer, prepare the necessary core, windings, insulating materials, fasteners, and assembly tools.
- Work Environment Preparation: Ensure the assembly workshop is clean, dry, well-ventilated, and has suitable temperature and humidity.
- Technical Documentation Preparation: Familiarize with the transformer’s design drawings, assembly process documents, and technical requirements.
- Personnel Preparation: Provide necessary training and technical briefings for personnel involved in the assembly to ensure they have the required skills and knowledge.
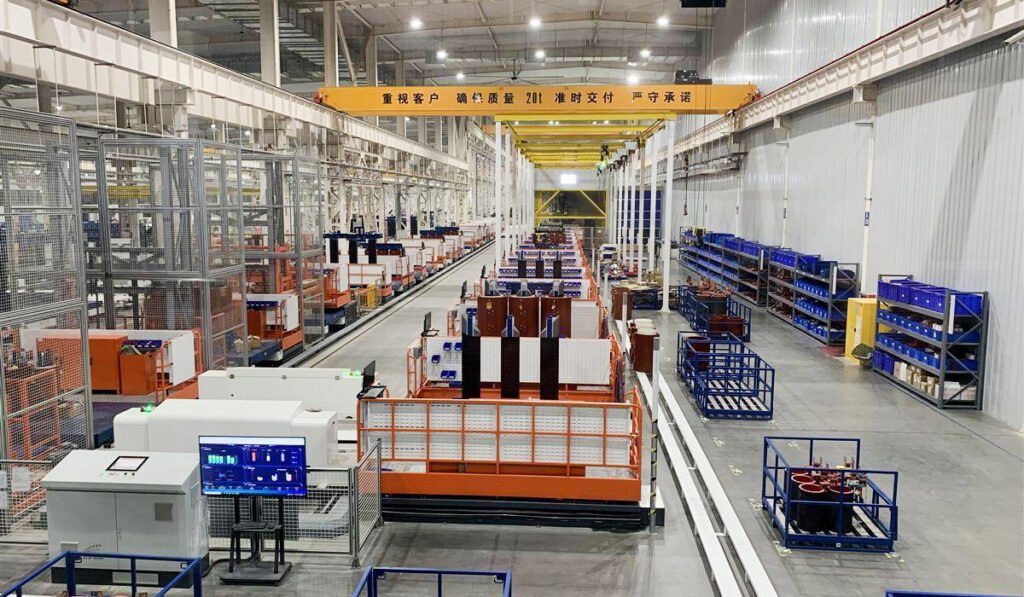
Assembly Process
The assembly process of dry type transformers typically includes the following key steps:
- Core Assembly: The core is the magnetic part of the transformer. During assembly, ensure that there are no gaps between the core laminations to avoid magnetic resistance and noise. Also, pay attention to the grounding and insulation treatment of the core.
- Winding Assembly: The windings are the electrical part of the transformer. During assembly, arrange, secure, and insulate the windings according to design requirements, paying attention to inter-layer, turn-to-turn, and ground insulation.
- Lead Assembly: The leads are the connection parts between the transformer and the external circuit. During assembly, ensure that the connections are secure and reliable, and pay attention to the insulation treatment and protective measures for the leads.
- General Assembly: After completing the assembly of the core, windings, and leads, proceed with the general assembly to ensure that all components are accurately positioned, securely fixed, and that the assembly has good sealing and protection.
Inspection and Testing After Assembly
After assembly is complete, rigorous inspection and testing are required, including:
- Visual Inspection: Check if the transformer’s appearance is neat, free from damage or deformation, and if all components are securely fastened.
- Insulation Resistance Test: Use an insulation resistance tester to test the insulation resistance, ensuring it meets design requirements.
- DC Resistance Test: Use a DC resistance tester to check the windings for any inter-turn short circuits or poor contacts.
- No-Load and Load Tests: Conduct no-load and load tests to check if the voltage ratio, no-load losses, and load losses meet design requirements.