The final assembly line for dry type transformers
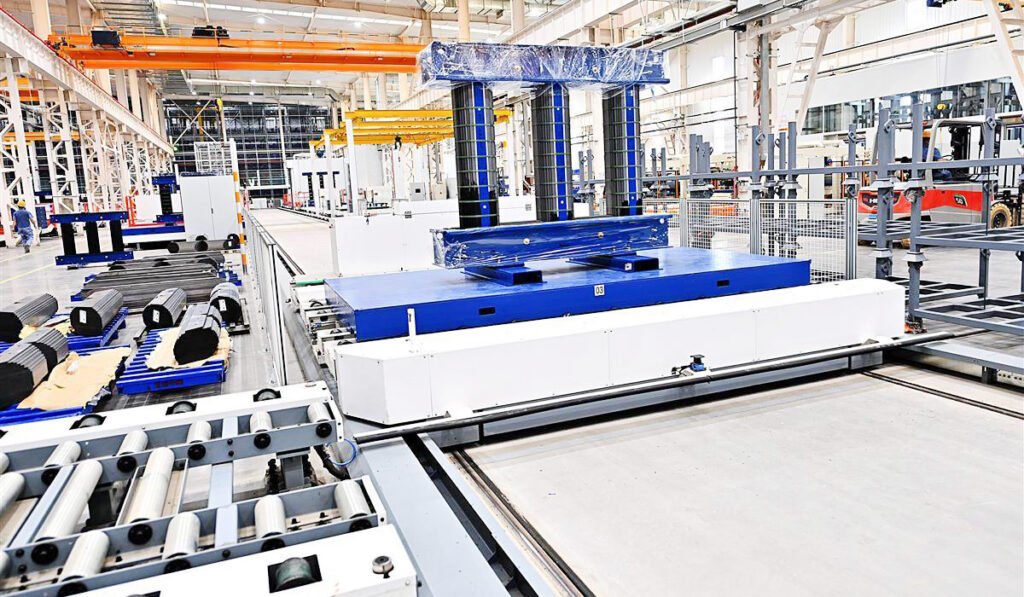
The final assembly line for dry type transformers is a crucial part of the transformer production process, involving multiple steps including raw material handling, winding production, potting, drying, assembly, and more. Here is a detailed introduction based on the search results:
Raw Material Storage Position
At the beginning of the assembly line, the raw material storage position is responsible for storing and managing all the raw materials needed for the production of dry type transformers. These materials include silicon steel sheets, copper wires, insulating materials, etc. The quality and quantity of raw materials directly affect the performance and reliability of the transformer.
High Voltage Winding Equipment
The high voltage winding equipment is specifically designed for making the high voltage windings of the transformer. In this stage, copper wires are precisely wound into the required shape and size. The equipment is designed to ensure that the copper wires remain taut during the winding process, preventing deformation.
Low Voltage Winding Equipment
The low voltage winding equipment is used for the production of the transformer’s low voltage windings. This equipment also needs to ensure precise copper foil winding, and the replacement of insulating and winding materials and molds is simple and efficient, enhancing production efficiency.
Potting Equipment
The potting equipment is used to pour insulating materials such as epoxy resin onto the windings and cores to form a solid insulation structure. This step is crucial for the insulation performance of the transformer.
Drying Equipment
After potting, the transformer needs to go through the drying equipment for curing and drying. This step ensures that the epoxy resin is fully hardened, guaranteeing the structural stability and electrical performance of the transformer.
Assembly Station
Once all components are produced, the assembly station is responsible for assembling the high voltage windings, low voltage windings, and other components into a complete transformer. This process requires precise and meticulous operations to ensure all parts are correctly installed and reliably connected.
Overhead Crane
Throughout the assembly line, the overhead crane plays a role in material transportation. It effectively moves materials and semi-finished products between various positions, ensuring a smooth and continuous production process.
Intelligent and Automated Systems
Modern dry type transformer assembly lines increasingly tend towards intelligent and automated systems. For example, Guilin Junte Fu电气’s high-end dry type transformer digital factory uses automated assembly lines and material transport vehicles, achieving automatic material distribution and automatic production at bottleneck processes. An intelligent system covers the entire factory, significantly improving factory space utilization and production capacity through digital transformation.
Summary
The final assembly line for dry type transformers is a complex and delicate production process involving multiple stages and equipment. With technological advancements, more and more production lines are adopting automation and intelligent technologies to improve production efficiency and product quality. The design and operation of these assembly lines are crucial for ensuring the performance and reliability of transformers.