Vacuum circuit breaker (VCB) assembly line layout

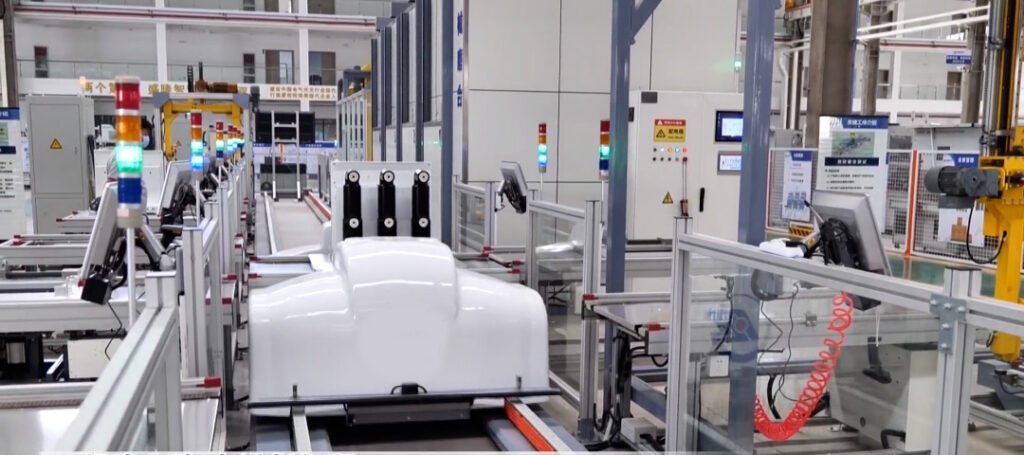
The assembly line layout for vacuum circuit breakers (VCBs) is characterized by high precision and strict control over environmental conditions to ensure the reliability and safety of the product. The VCB assembly line layout and the advantages of using 3D design layouts in assembly and testing processes:
Assembly Line Layout Features
- High Automation
- The assembly line typically employs automated machinery and robotic technology for precise assembly work, reducing human errors and increasing production efficiency.
- Cleanroom Environment
- As the vacuum arc chamber of VCBs needs to operate in a high vacuum environment, the assembly line must be conducted in a cleanroom to prevent dust and contaminants from affecting vacuum levels and electrical performance.
- Strict Quality Control
- Quality checkpoints are present after each assembly step to ensure the correct installation and functional performance of each component.
- Dedicated Testing Areas
- After assembly, VCBs require electrical performance testing in dedicated areas, including insulation tests, circuit interruption tests, and reliability tests of the operating mechanism.
- Environmental Simulation
- The assembly line simulates various environmental conditions, such as temperature, humidity, and pressure changes, to ensure that VCBs can operate stably under different working environments.
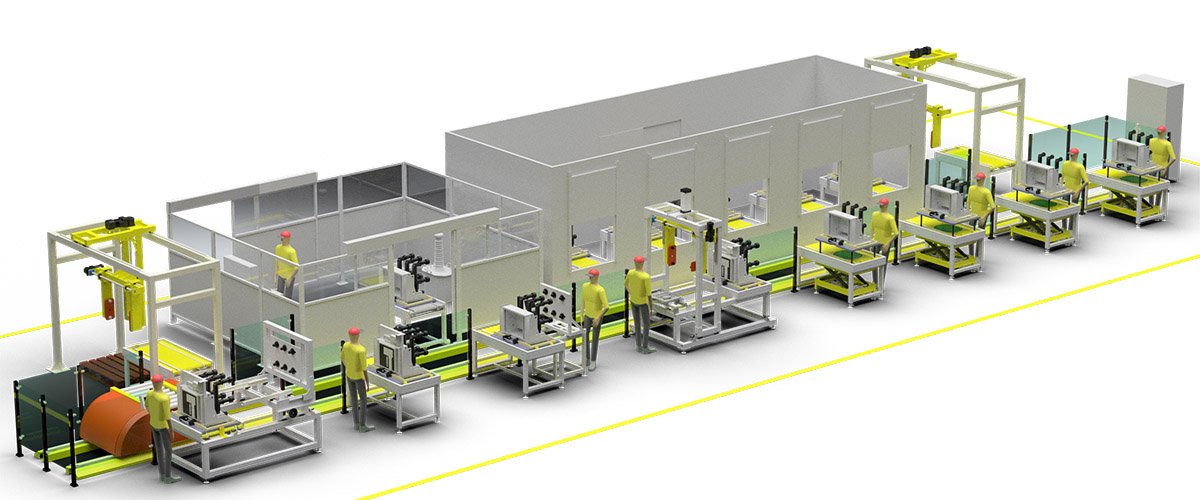
Advantages of 3D Design Layout
- Accurate Spatial Planning
- 3D design allows engineers to simulate the assembly line layout in a virtual environment, optimizing space utilization and reducing adjustments and rework during actual assembly.
- Visualization and Communication
- The 3D model provides an intuitive visual display, facilitating communication and understanding among team members, ensuring that each step is executed accurately according to the design drawings.
- Simulation and Optimization
- Before actual assembly, the entire assembly process can be simulated to identify potential issues and bottlenecks, allowing for optimization and adjustments in advance.
- Reducing Errors and Increasing Efficiency
- By using 3D design, layout-related errors can be minimized, improving the efficiency and quality of the assembly line.
- Ease of Maintenance and Upgrade
- The 3D model is easy to document and archive, providing detailed reference information for future maintenance and upgrade work.
The features of the VCB assembly line layout and the advantages of using 3D design layouts together ensure the high quality of the product and the efficiency of production. Through precise assembly and testing processes, supported by 3D design technology, VCBs can meet strict industrial standards and performance requirements.