The welding process for the gas chamber of a ring main unit
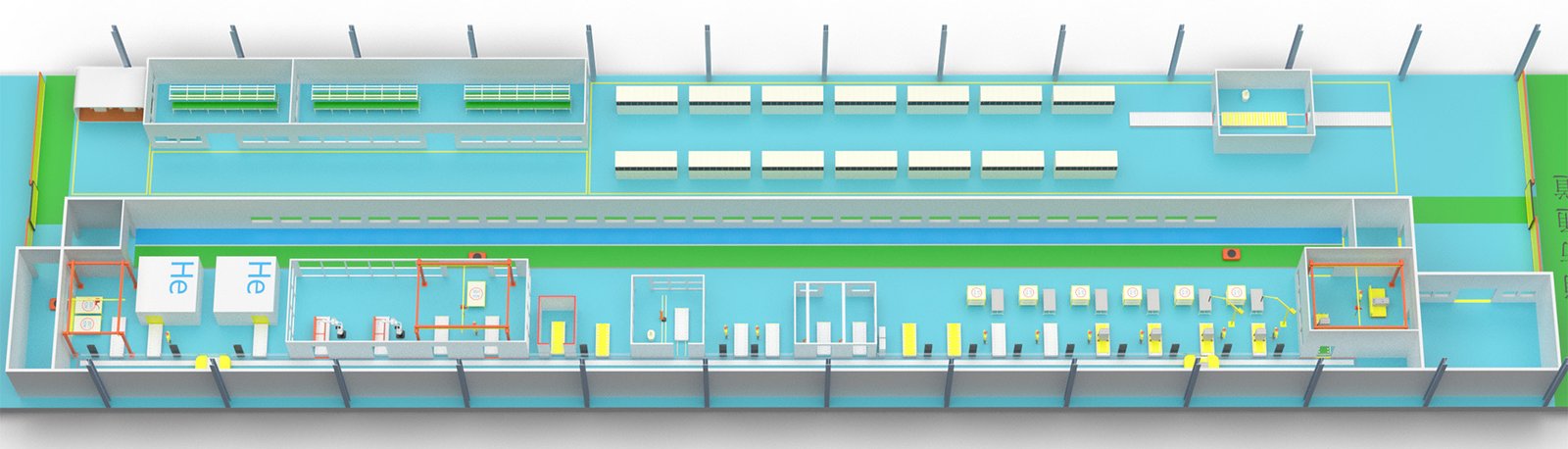
The gas chamber in a ring main unit is critical for its safety and longevity. Manufacturers and technicians should prioritize its welding quality using scientific methods and equipment. Common welding equipment includes arc, gas-shielded, and laser machines. Techniques like TIG, MIG/MAG, and submerged arc welding are used for high-quality, uniform, and deep welds. Issues like bubbles, cracks, and deviations are addressed by adjusting gas flow, welding speed, temperature, and voltage.
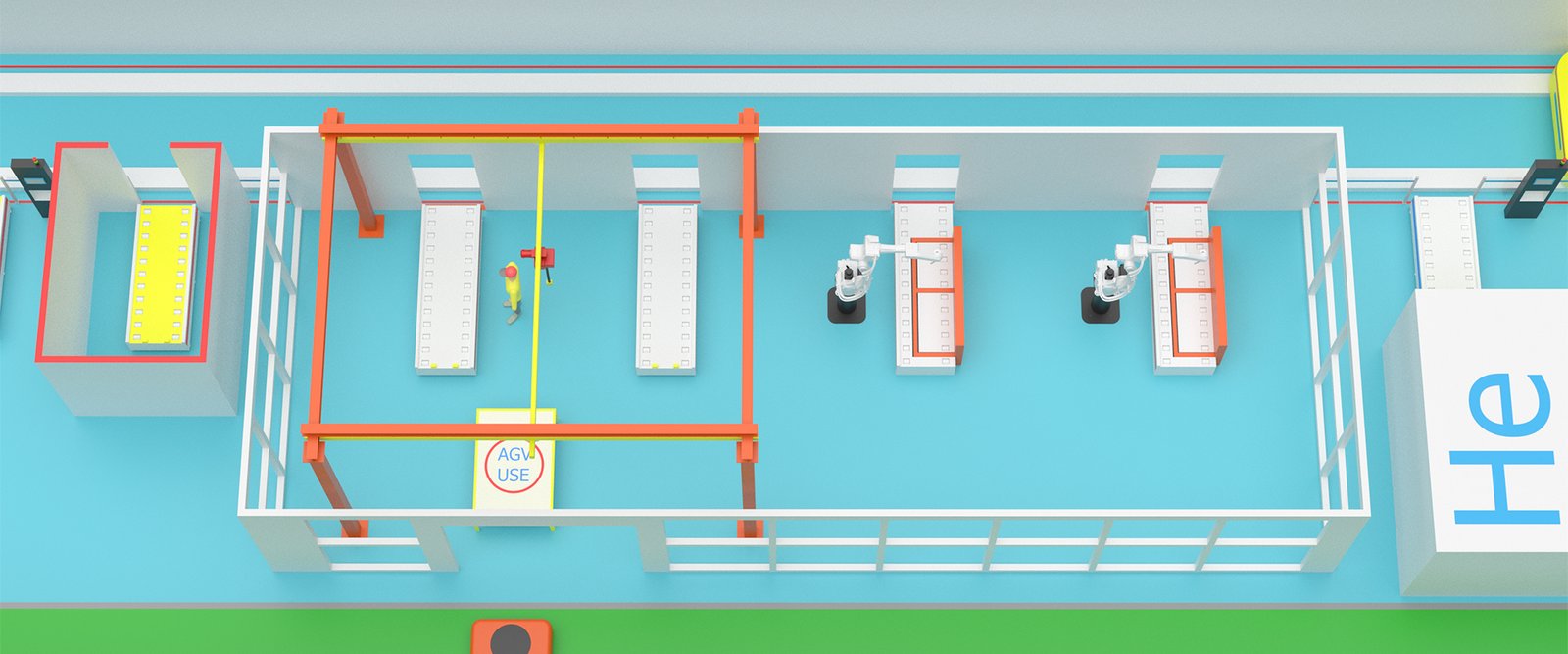
I. General Overview
The gas chamber of a ring main unit is an essential component of the unit, and its welding quality directly affects the safety and service life of the ring main unit. Therefore, manufacturers of ring main units and technical personnel engaged in welding processes should pay attention to the welding techniques of the gas chamber, adopt scientific and reasonable welding methods and equipment to ensure the quality of the welding.
II. Welding Equipment
The welding equipment for the gas chamber of a ring main unit includes arc welding machines, gas-shielded welding machines, and laser welding machines, among others. The gas-shielded welding machine is the most widely used because it can protect the welding area from oxidation and contamination, thereby improving the quality of the welding.
III. Welding Methods
The main welding methods for the gas chamber include TIG (Tungsten Inert Gas) welding, MIG/MAG (Metal Inert Gas/Metal Active Gas) welding, and submerged arc welding. TIG welding is a type of inert gas welding with a melting electrode, which can produce high-quality welds and has a fast welding speed. MIG/MAG welding is a versatile gas-shielded welding method suitable for welding thicker metal materials and can produce uniform welds. Submerged arc welding is an efficient welding method that can produce larger welds and deeper penetration.
IV. Welding Structure
The gas chamber of a ring main unit generally adopts a box structure, and the welding methods can include longitudinal welding, transverse welding, or circumferential welding. Among them, circumferential welding is a commonly used method that can produce welds with high strength and sealing performance.
V. Common Problems and Solutions
- Bubbles appeared during the welding of the gas chamber.
Solution: Increase the gas flow or reduce the welding speed.
- Cracks appeared in the weld.
Solution: Check if the welding temperature is too high or the welding speed is too fast.
- Weld deviation.
Solution: Adjust the welding current, voltage, or tap the welding area.