Technical characteristics and assembly testing precautions of VCB
Vacuum Circuit Breakers (VCBs) are widely used in power systems due to their excellent performance and unique technical characteristics. Here are the technical features and key points to consider during the assembly and testing of VCBs:
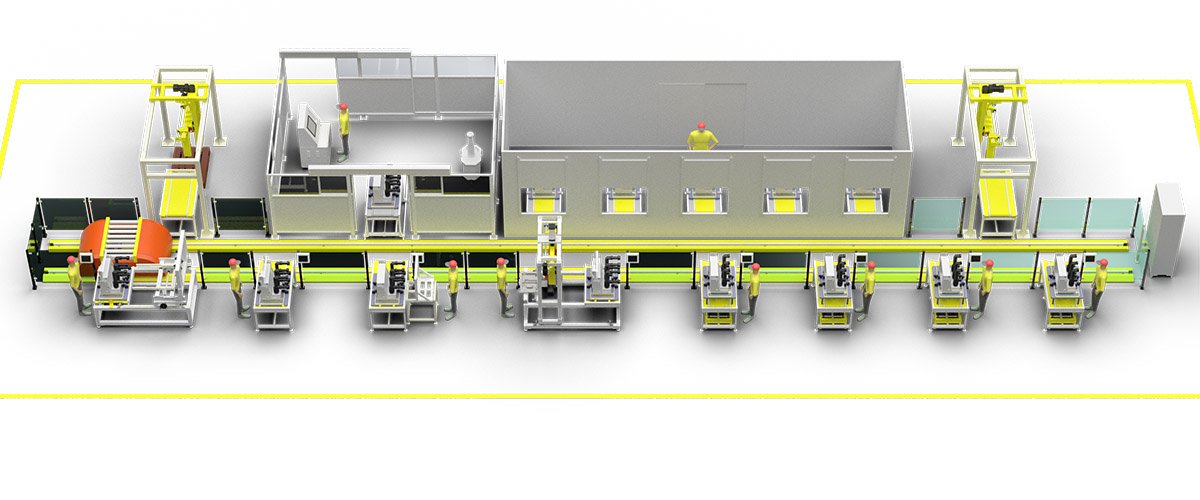
Technical Features:
- High Voltage and High Capacity: VCB technology has evolved to handle voltage levels up to 126kV and high-capacity loads.
- Miniaturization: Through the use of new arc control technologies and composite insulating techniques, the size and weight of VCBs have been significantly reduced.
- Intelligence: Modern VCBs are trending towards integrating intelligent functions such as self-diagnosis, status monitoring, and remote control.
- Low Overvoltage: By using special contact materials and designs, VCBs generate lower overvoltage when breaking small currents.
- Maintenance-Free: The design of VCBs reduces maintenance requirements and extends the service life of the equipment.
- Specialization and Multifunctionality: VCBs can be customized according to specific application requirements, such as synchronous operation and low overvoltage operation.
- High Mechanical and Electrical Life: Due to the fast arc extinction in a vacuum environment, the wear on the contacts of VCBs is minimal, resulting in a long mechanical and electrical life.
- Rapid Response: VCBs have fast closing and opening speeds, allowing for a quick response to fault conditions in the power grid.
- Environmentally Friendly: VCBs do not use harmful gases such as SF6, making them more environmentally friendly.
Assembly and Testing Considerations:
- Safety Measures: During high-voltage testing, it is essential to set up barriers and have a designated person supervise to ensure the safety of the operators.
- Discharge Handling: After measuring the insulation resistance, the test specimen should be fully discharged to prevent electric shock hazards.
- Pre-test Preparation: Ensure that all instruments, meters, and equipment are ready and conduct a hazard analysis.
- Run-in Test: After assembly, VCBs should undergo a run-in test to ensure that mechanical characteristic indicators meet the requirements.
- Vacuum Degree Testing: Regularly use a vacuum tester to perform qualitative tests on the vacuum degree of VCBs to ensure it meets the requirements.
- Withstand Voltage Test: Perform AC withstand voltage and impulse withstand voltage tests on VCBs to verify their insulation strength.
- Mechanical Characteristic Testing: Test the opening distance, contact travel, and mechanical characteristics of VCBs to ensure they meet technical requirements.
- Connection Check: Inspect all connections for looseness to ensure reliable connections.
- Lubrication Maintenance: Lubricate moving joints and sliding parts to reduce wear.
- Resistance Testing: Perform DC resistance testing on VCBs used for high-current operations to ensure good electrical contact in the conductive circuit.
- Characteristic Test: After replacing the vacuum tube, conduct mechanical characteristic testing and withstand voltage tests.
- No-load Operation: Perform continuous no-load operations after the annual inspection and before commissioning to ensure the VCB operates normally.
- Monitoring of Reduced Vacuum Degree: Regularly monitor the vacuum degree of VCBs to detect and address issues of reduced vacuum degree promptly.
By following these technical features and assembly testing considerations, the performance and safety of vacuum circuit breakers can be ensured, improving their reliability and efficiency in power systems.