Power Transformer Assembly Production Line
The process flow of transformer production line mainly includes the following key steps:
1. Coil winding:

Installation of winding frame: First, it is necessary to install the winding frame, which is the foundation of coil winding.
Winding coil: Wrap wires on the skeleton to form the coil part of the transformer.
Wire welding: Weld the wound coil to ensure the firmness of the connection.
Insulation: Insulate the coil to prevent short circuits and electrical breakdown.
Coil shaping: Adjust the shape of the coil to meet the design requirements.
Coil testing: Electrical performance testing of the coil to ensure compliance with technical standards.
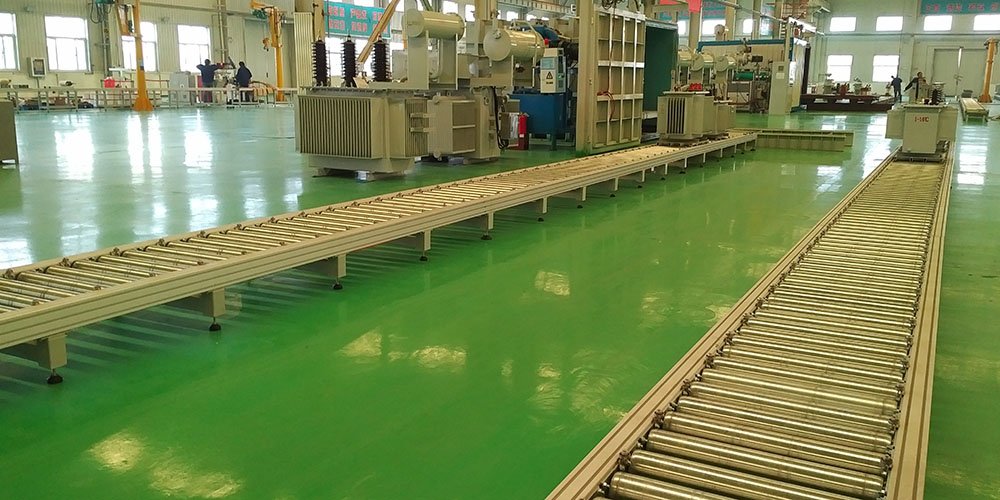
2. Iron core assembly:
Silicon steel sheet cutting: Cut the silicon steel sheet into the required size.
Deburring: Process the edges of silicon steel sheets to remove burrs.
Stacking iron core: Stack the cut silicon steel sheets according to the design requirements.
Install pull plates and shields: Install pull plates and shields to secure the iron core and reduce eddy current losses.
Tie the iron core: Fix the iron core with straps to ensure its structural stability.
Iron core test: Conduct performance testing on the assembled iron core.
Install iron core clamp: Install the iron core into the clamp of the transformer.
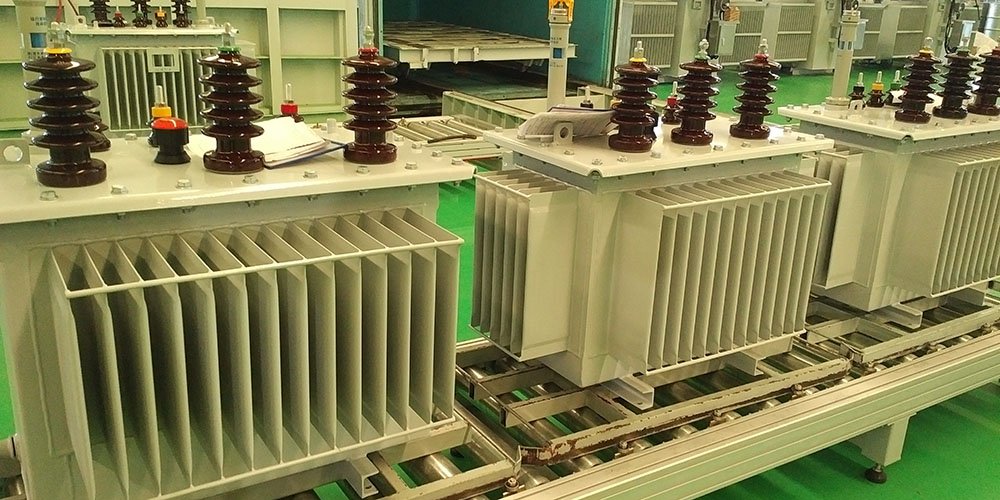
3. Insulation processing:
Insulation cutting: Cut insulation materials according to design requirements.
Deburring: Process the edges of insulation components to ensure they are smooth and free of burrs.
Chamfer: Chamfer the edges of insulation components to reduce stress concentration.
Moisture proof treatment: Apply moisture proof treatment to insulation components to improve their moisture resistance performance.

4. Processing of oil tanks and storage tanks:
Steel plate cutting: Cut the steel plate according to the design drawings.
Welding of fuel tank and oil storage tank: Weld the cut steel plate into the fuel tank and oil storage tank.
Rust removal: Remove rust from welds and surfaces.
Sandblasting: Sandblasting the surface of the fuel tank to improve the adhesion of the paint film.
Primer: Apply primer on the surface of the fuel tank to protect the steel plate from corrosion.
Spray painting: Spray painting the fuel tank to improve appearance quality and anti-corrosion performance.
Mechanical strength test: Conduct a strength test on the fuel tank to ensure that it meets safety requirements.
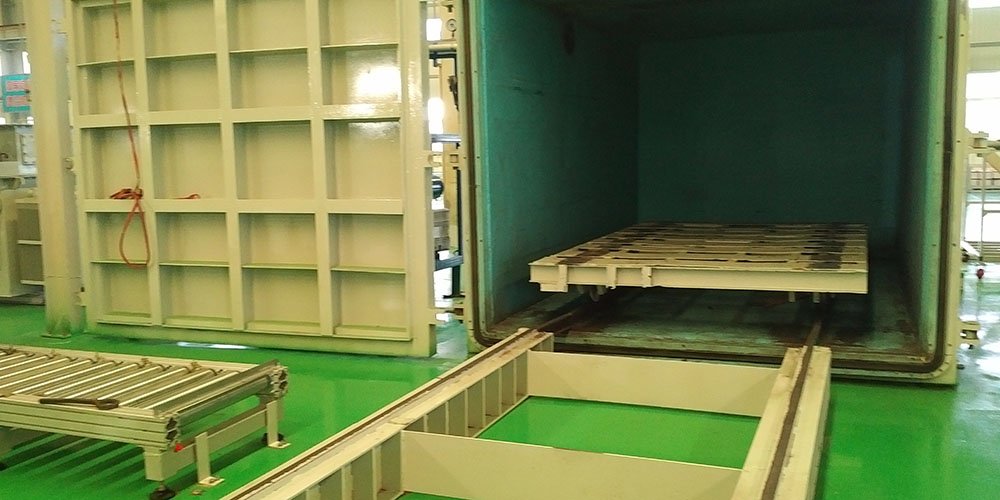
5. General assembly:
Install iron core: Install the iron core into the main structure of the transformer.
Installing fuel tank pipelines: Installing fuel tanks and related piping systems.
Wrap the coil: Wrap the coil onto the iron core.
Stacking iron yokes: Stack the iron yokes onto the iron core.
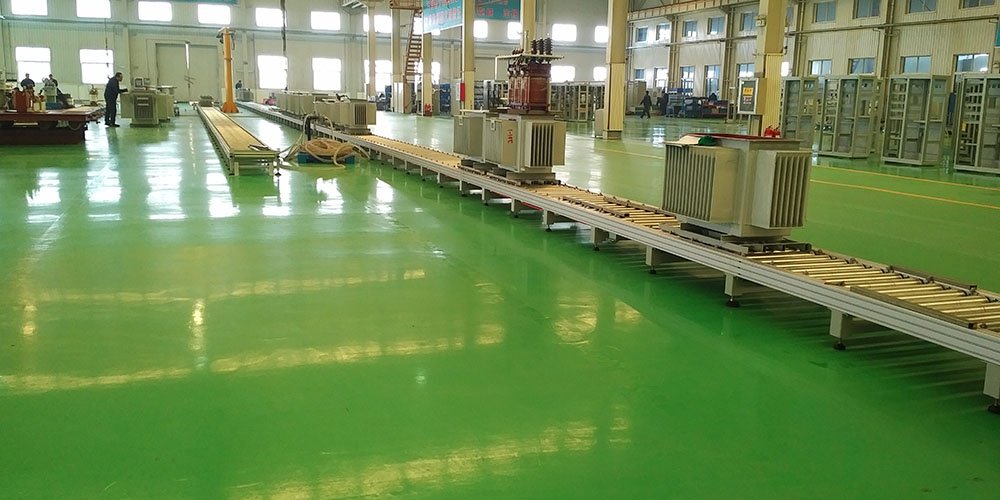
Install tap changer: Install tap changer to adjust the output voltage of the transformer.
Welding lead: The lead that connects the welding coil to the outside.
Wrap lead insulation: Insulate the soldered leads.
Semi finished product test: Conduct performance testing on semi-finished transformers.

Body drying: Dry the transformer body to remove moisture.
Organize the transformer body: Organize the transformer body to ensure a clean appearance.
Oil tank assembly: Assemble the oil tank and transformer body together.
Attachment assembly: Install various accessories for transformers, such as thermometers, pressure relief valves, etc.
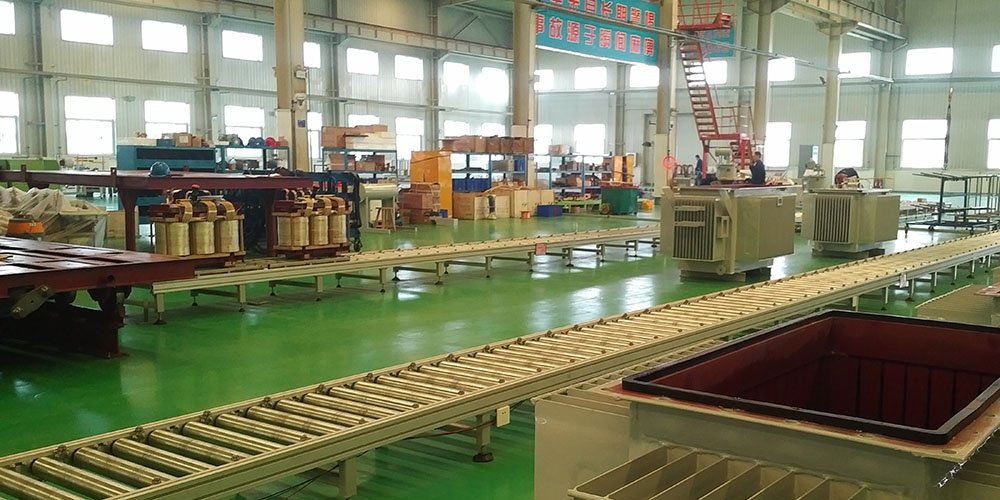
Oil injection: Inject insulating oil into the fuel tank.
Sealing test: Conduct a sealing performance test on the fuel tank.
Hot oil circulation: Through the hot oil circulation system, ensure uniform oil temperature and improve insulation performance.
Quiet: Let the transformer stand for a period of time to stabilize its performance.