Modular technology for assembly production lines of high-voltage electrical products
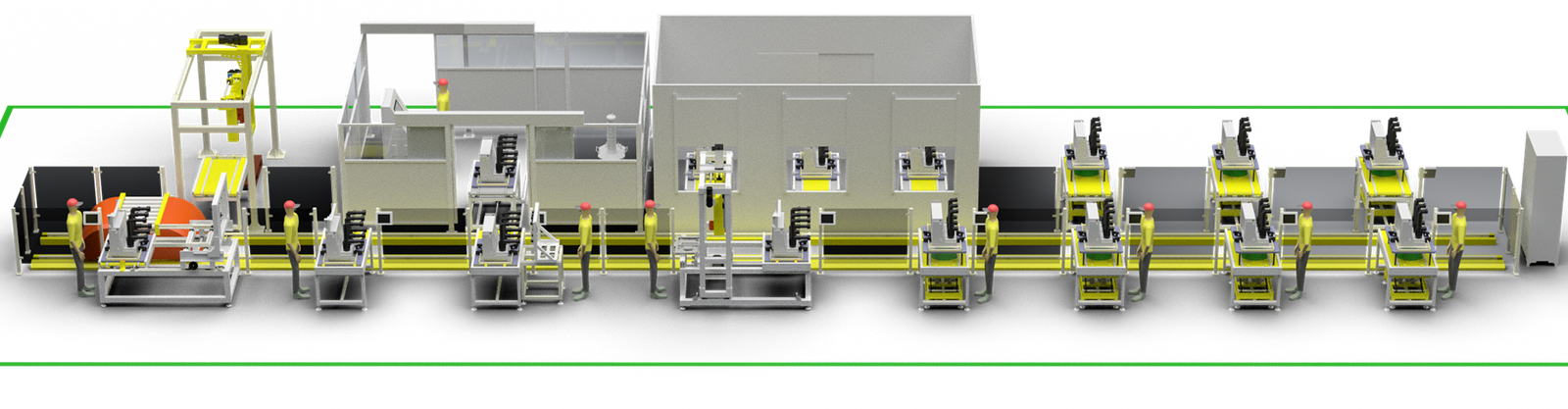
The benefits of adopting modular design and implementation in assembly lines are mainly reflected in the following aspects:
1. Improve production efficiency
Modular assembly lines allow each process or workstation to operate independently, allowing for parallel processing of multiple tasks, thereby improving overall production efficiency. Each module can focus on specific production processes, achieving rapid production and efficient operation through optimized design and process flow.
2. Flexibility and Scalability
Modular design allows the assembly line to quickly adjust according to changes in production demand. When new production capacity needs to be added or production processes need to be changed, modules can be easily added or reconfigured without the need for large-scale modifications to the entire assembly line.
3. Reduce costs
Modular assembly lines reduce reliance on a single large equipment and lower capital expenditures. Meanwhile, due to the standardization and universality of modules, maintenance and repair costs can be reduced, as well as material waste in the production process.
4. Quality control
Each link of the modular assembly line can be independently controlled for quality to ensure that the output of each module meets the standards. This decentralized quality control mechanism helps to detect and solve problems in a timely manner, ensuring the quality of the final product.
5. Easy to maintain and upgrade
Modular design makes maintenance and upgrading of assembly lines easier. When a module needs maintenance or upgrade, it will not affect the operation of the entire assembly line, thereby reducing downtime.