
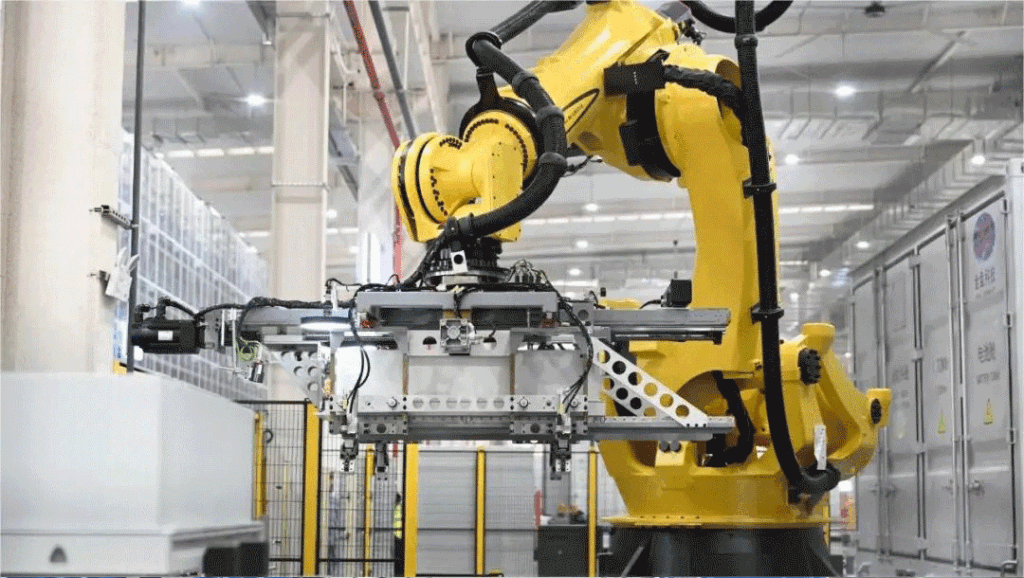
The final assembly process of dry type transformers is a complex procedure that involves multiple steps to ensure the quality, performance, and reliability of the transformer.
Assembly Process Flow
- Core Assembly The core, which is the primary magnetic part of the transformer, is typically made from high-silicon hot-rolled or cold-rolled silicon steel sheets that are stacked or wound. During core assembly, it is important to ensure precise alignment of the core limbs and yokes, as well as the uniformity and stability of the core.
- Winding Installation Winding, the electrical part of the transformer, is made from insulated flat wires or round wires. When installing the windings, it is crucial to ensure they are wound evenly and tightly, and the insulation type is chosen to be either impregnated or resin insulated to enhance insulating properties.
- Insulating Tube Placement Insulating tubes are placed between the high and low voltage windings to increase electrical insulation. The material and size of the insulating tubes need to be carefully selected according to the design requirements of the transformer.
- Winding Support and Constraint Use padding blocks to support and constrain the windings, ensuring the accurate positioning of the windings inside the transformer and reducing vibration and noise during operation.
- Tightening Component Anti-loosening Treatment Anti-loosening treatment is applied to the fasteners that connect the various components of the transformer to ensure the stability of the transformer during long-term operation.
- Final Assembly Completion and Testing After all components are installed, a final assembly check and testing are conducted. This includes visual inspection, insulation resistance testing, DC resistance testing, and no-load and load tests to ensure the performance of the transformer meets the design requirements.
Equipment Composition
- Automated Assembly Line The assembly line typically includes automated machinery and robotic arms to improve assembly efficiency and precision, reducing the need for manual operations.
- Vacuum Pressure Impregnation (VPI) Equipment Used for vacuum pressure impregnation treatment of the windings to enhance their insulating properties and moisture resistance.
- Testing and Inspection Equipment Include insulation resistance testers, DC resistance testers, and other devices used to test the performance of the completed transformer.
- Environmental Simulation Equipment Simulates the operating conditions of the transformer under different environmental conditions to ensure stable operation across various settings.
- Cooling System For transformers using forced air cooling, a cooling system with fans and heat dissipation devices is required.
- Temperature Control System Installed with an automatic temperature control and protection system to monitor and regulate the temperature of the transformer, ensuring it operates within a safe temperature range.