Automation equipment used for assembling and producing current transformers and voltage transformers

The current transformer (CT) and voltage transformer (VT) in the switchgear are key components used for measurement and control in the power system. Their production process usually includes the following main steps:
1. Design and Engineering Preparation
Before production, detailed design work needs to be carried out according to technical specifications and performance requirements. This includes selecting appropriate materials, determining dimensions, calculating winding turns, and designing insulation structures. At the same time, it is necessary to prepare production drawings and process documents.
2. Material selection and processing
The core materials of transformers include silicon steel sheets, winding wires, insulation materials, etc. Silicon steel sheets are used to make iron cores, winding wires are used to make primary and secondary windings, and insulation materials are used to ensure the safe operation of equipment.

3. Iron core manufacturing
The iron core is the core part of a transformer, usually composed of multiple layers of silicon steel sheets stacked together. In the manufacturing process, it is necessary to make the iron core through steps such as stamping, lamination, and binding, and ensure its compact structure to reduce hysteresis and eddy current losses.
4. Winding production
The winding is a crucial part of a transformer for transmitting information. The primary winding of the current transformer is connected in series in the circuit, and the secondary winding is connected in parallel on the measuring equipment; The primary winding of the voltage transformer is connected in parallel in the circuit, and the secondary winding is used to output voltage signals. The production of windings requires precise winding technology and strict control of the number of turns.
5. Assembly and insulation treatment
Assemble the prepared iron core and winding together and perform insulation treatment to ensure the electrical safety of the transformer. Insulation treatment may include vacuum pressure impregnation (VPI) process to improve insulation performance and moisture resistance.
6. Testing and Calibration
After the assembly of the transformer is completed, a series of tests are required, including electrical performance testing, insulation strength testing, and error calibration. These tests ensure that the transformer meets the specified technical parameters and performance standards.
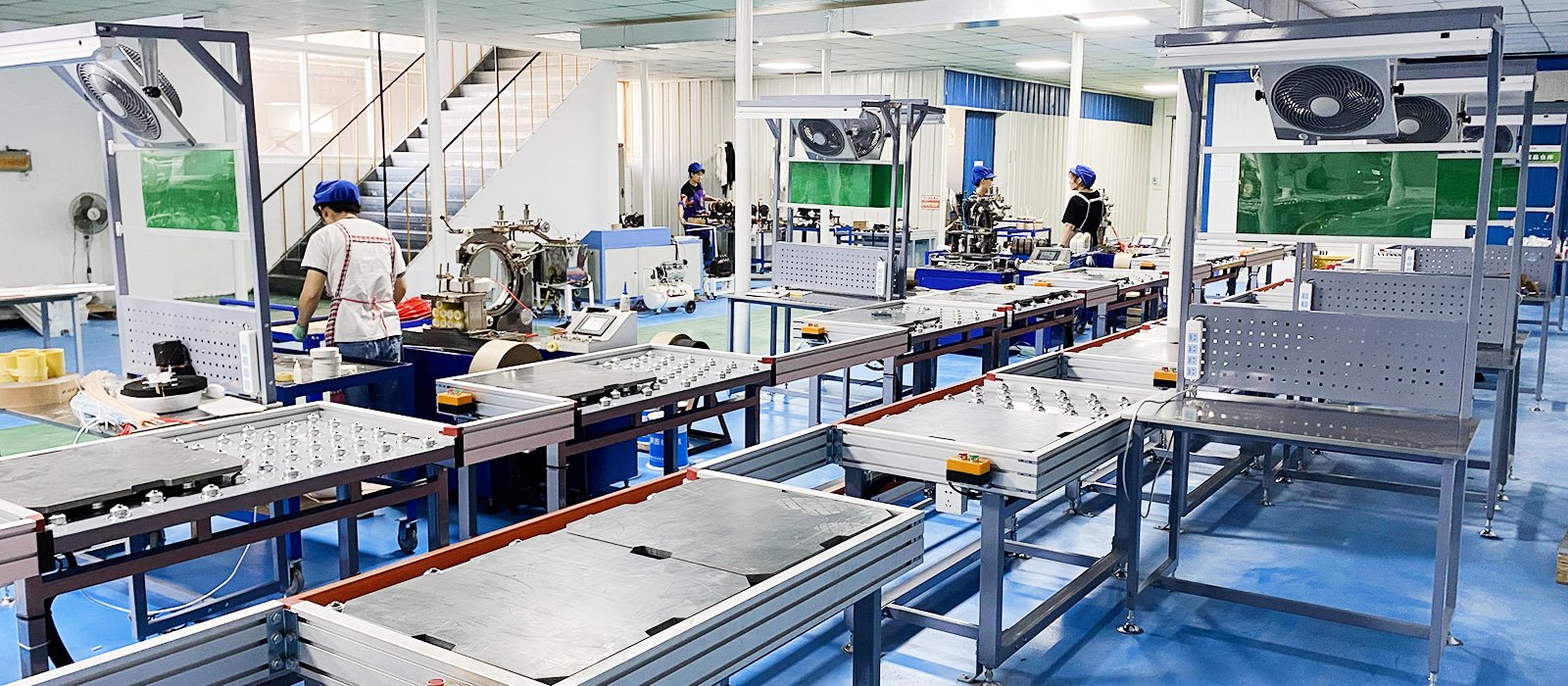
7. Shell manufacturing and assembly
Transformers typically require a sturdy casing to protect internal components from external environmental influences. The selection and processing of shell materials need to consider factors such as mechanical strength, environmental resistance, and heat dissipation.
8. Final inspection and packaging
Before the transformer leaves the factory, a final quality inspection is required, including visual inspection, performance retesting, etc. After confirming accuracy, pack appropriately for transportation and storage.
The entire production process requires strict quality control to ensure the reliability and accuracy of transformers. The introduction of automated production lines has improved production efficiency and product consistency.